2016-04-25
Friction is a critical limiting factor in
determining the type and length of cable
installation. Although very little
information on cable installation is provided in this
guide, this section has been made available
as a background reference on frictional
properties.
Definitions
Friction:the nature of interaction
occurring between two surfaces. The basis of
friction has its roots in the mechanical
and physical-chemical makeup of the
interface created by bringing together two
surfaces.
Coefficient of friction, COF:the ratio of
the force required to move a body relative to
the normal, or clamping force, acting to
keep the bodies together.
Static COF:the ratio of forces required to
bring about the onset of motion between
two bodies at rest with each other.
Kinetic COF:the ratio of forces acting on a
body already in motion. It is essentially a
measure of the effort required to keep the
body in motion.
Friction Reduction
Friction reduction can be promoted by
reducing mechanical interactions, grounding
electrostatic charges, reducing polar
interactions, selecting dissimilar polymers, and
employing methods and mechanisms which act
to dissipate heat. Although many
Chapter 14
Duct and Conduit
499
times little can be done to control the
composition of cable jacket materials, choices
can be made to select friction-reducing
conduit designs and lubricating mechanisms.
The use of lubricants is strongly
recommended during the placement of the conduit
or cable, or may be included in the
manufacturing process of the conduit. Typical
lubrication methods would include:
Water-soluble lubricantsare available in
many different forms including low
viscosity free-flowing petuitous liquids,
creamy consistencies, and stiff gels. Low
viscosity liquids are best suited for
placement of long lengths of lightweight cables,
such as fiber cables. Heavier, cream-like
consistencies are useful on lightweight
power conductors. Stiff gels are used in
vertical applications in buildings, or where
high sidewall loads are expected in
placement of heavy power cables or innerducts.
Polymeric water-soluble lubricantsare
commonly used in the field to lubricate the
placement of cable, or of the conduits
themselves. In this case the lubricant is applied
either ahead of, or in conjunction with,
the advancing cable. Water-soluble polymer
chemistries include a number of different
enhancements including surface wetting
and cling, modification via fatty acids or
their derivatives, or by inclusion of various
friction-reducing oils, including
silicones.
Conduits may be pre-lubricatedduring the
manufacturing process by incorporation
of lubricants directly onto the conduit
inner wall, or via a lubricant-modified
coextruded layer. The most common type of
lubricant used for this type of
application is silicone polymer, although
other agents such as mineral oils, fatty acid
derivatives and glycols have also found
use.
Prelubrication finds particular value with
fiber cable push-blow systems. Because
the sidewall loads with these techniques
are quite low compared with pulling,
and the distances so great, the viscous
drag contributed by water-soluble lubes
can be detrimental. The ultra-light amount
of lubricants employed by factory prelubrication methods can be a real advantage.
Geometry of the inner surface of the
conduit can also play a role in friction
reduction. As the normal load increases,
the COF is found to decrease, unless the
surface is damaged in such a way so as to
increase the contact area, or heat is allowed
to build up at a rate faster than it can be
conducted away. Ribs formed on the inner
conduit wall are a common design feature to
reduce friction.
Longitudinal ribbingresults in a reduction
of the contact surface between the cable
and the conduit wall from an area to a line
of contact. Decreasing the area of contact
under the same sidewall load results in a
higher localized normal force. Within a
limited range of sidewall loads, the COF is
found to go down – at least until the
loading causes localized damage to the
jacket sheath.
Chapter 14
Duct and Conduit
500
Spiral ribbingfurther reduces the contact
area from a line to a series of points. In
addition, because the advancing cable is
alternately on and off the ribbing, there is
an opportunity for cooling and
re-lubrication. Constantly changing the direction of
the spiral eliminates the tendency to
accumulate spiral-induced torque in the cable.
Transverse ribbing,or corrugated profiles,
results in similar friction reducing
geometries. However, there is a tendency
for field-added lubrication to be scraped
off the cable by the corrugations. In
addition, the high degree of flexibility requires
careful placement of the duct to reduce the
buildup of friction due to path curvature.
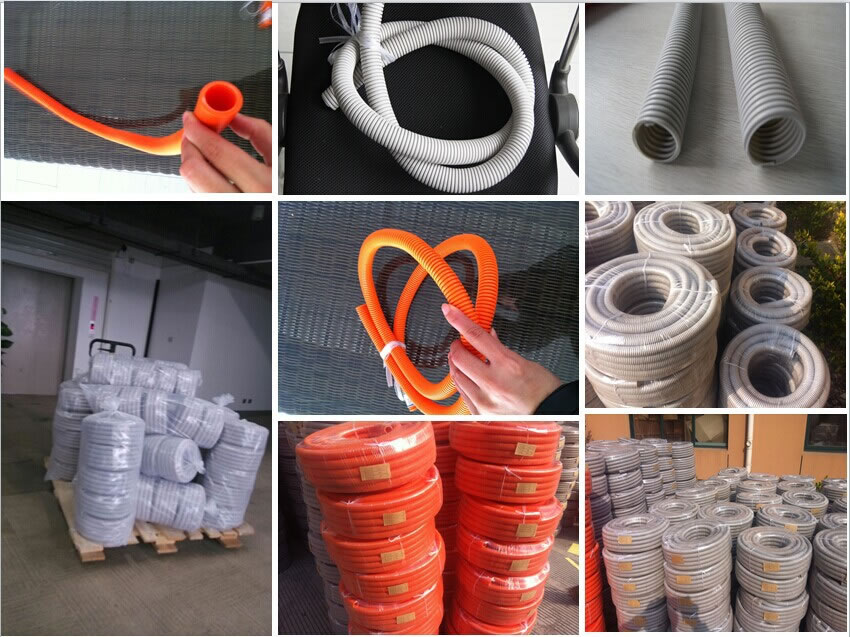
Conduit Network Pulling
Cable Dimension Considerations